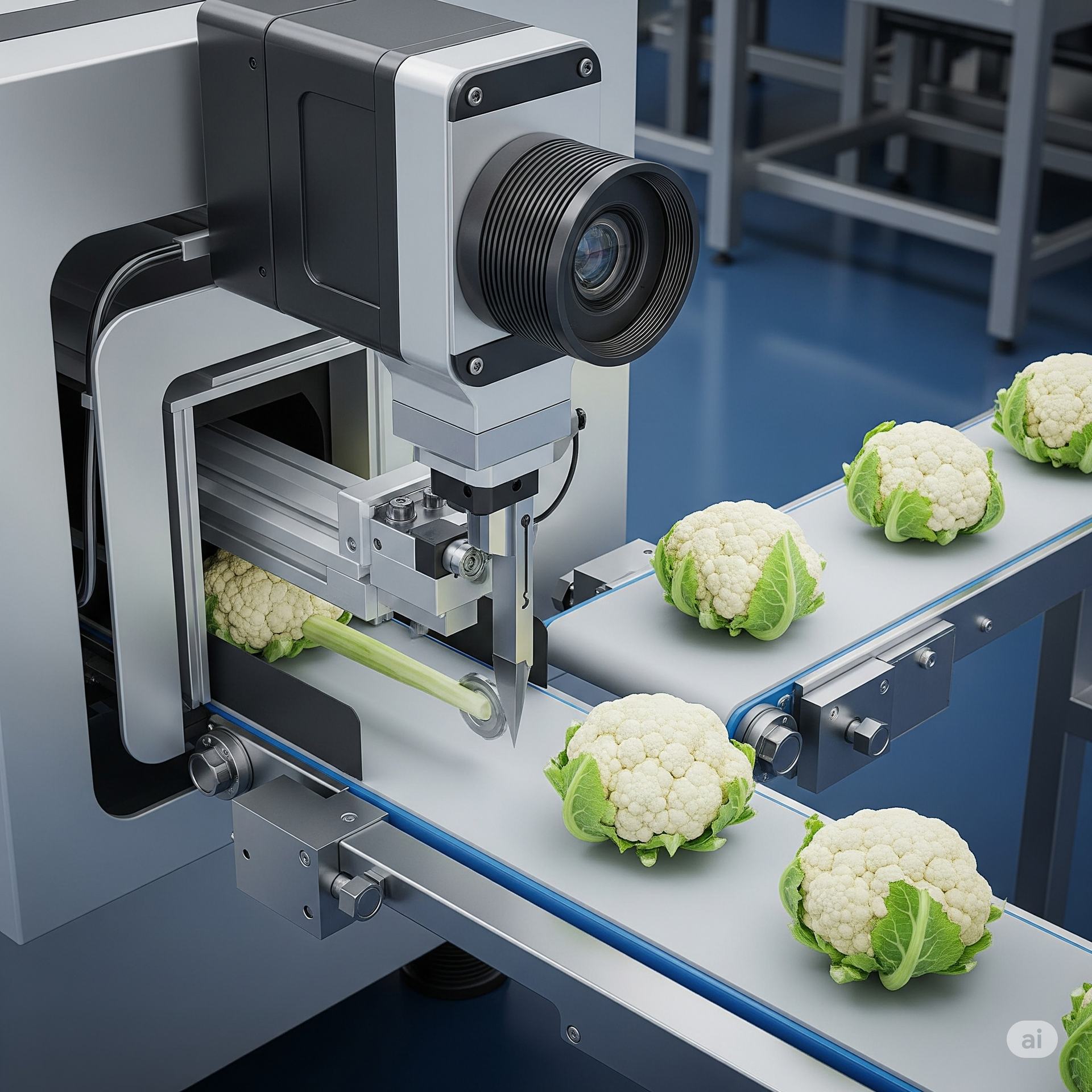
Cauliflower Stem Cutting Machine
Case Study: Image Processing-Based Automated Cauliflower Stem Cutting
Introduction
The agricultural and food processing industries are continually seeking innovative solutions to enhance efficiency, reduce labor costs, and improve product consistency. In the processing of vegetables like cauliflower, manual stem cutting is a labor-intensive, time-consuming, and often inconsistent task. Variations in cauliflower size, shape, and stem length necessitate human judgment, leading to potential inefficiencies and product waste. This case study explores the successful implementation of an image processing-based automated system designed to precisely measure and cut cauliflower stems, streamlining the packing process.
Problem Statement
Traditional cauliflower stem cutting methods present several challenges:
Labor Intensive: Requires a significant workforce, increasing operational costs, especially during peak seasons.
Inconsistency: Manual cutting is prone to human error, leading to variations in stem length, which affects product uniformity and packaging efficiency.
Reduced Throughput: The speed of processing is limited by human operators, creating bottlenecks in the production line.
Waste Generation: Inaccurate cuts can result in excessive stem removal (product loss) or insufficient trimming (requiring re-work).
Hygiene Concerns: Direct human contact can introduce contamination risks.
There was a clear need for an automated solution that could provide precise, consistent, and high-throughput stem cutting while minimizing waste and human intervention.
Proposed Solution: Automated Vision-Guided Stem Cutting
Our solution involves an integrated system that leverages advanced image processing and automation to precisely trim cauliflower stems. The core components of the system include:
Conveyor Belt System: Transports cauliflowers in individual trays.
High-Resolution Camera: Captures images of each cauliflower as it passes a designated inspection point.
Image Processing Software: Analyzes the captured images to determine cauliflower dimensions and precisely locate the optimal stem cutting point.
Automated Cutter: A precision cutting mechanism (e.g., a robotic blade or waterjet) executes the cut based on the image processing data.
Ejection/Transfer Mechanism: Moves the trimmed cauliflower to the packing station.
Methodology
System Architecture:
Input: Cauliflowers are manually or automatically placed into individual, uniformly sized trays on a continuous conveyor belt.
Image Acquisition: As each tray moves under a fixed gantry, a high-resolution industrial camera, equipped with appropriate lighting (e.g., diffuse LED lighting to minimize shadows), captures a top-down image of the cauliflower. The camera is calibrated to ensure accurate spatial measurements.
Image Processing & Analysis: The captured image is immediately transmitted to a dedicated industrial PC running custom image processing software. The software performs the following steps:
Pre-processing: Noise reduction, contrast enhancement.
Segmentation: Isolating the cauliflower head and stem from the background and tray. This often involves color thresholding, edge detection, or more advanced machine learning-based segmentation techniques.
Feature Extraction:
Dimension Measurement: The software calculates the overall diameter and height of the cauliflower head.
Stem Detection: Algorithms identify the stem's base and its connection point to the florets. This is critical for determining the ideal cut location, which aims to leave a minimal, aesthetically pleasing stem length while ensuring the head remains intact.
Orientation Analysis: If necessary, the system can also determine the orientation of the cauliflower to guide the cutter for optimal access.
Decision Logic: Based on pre-defined parameters (e.g., desired stem length, acceptable head diameter), the software calculates the precise coordinates and angle for the cut.
Automated Cutting: The calculated cutting parameters are sent to a robotic arm equipped with a cutting tool (e.g., a rotating blade or a high-pressure waterjet). The robotic arm moves precisely to the determined location and executes the cut.
Output: The trimmed cauliflower is then pushed or transferred from its tray onto another conveyor belt or directly into a packing unit. The discarded stem falls into a waste collection bin below.
Calibration and Training:The system requires initial calibration using known cauliflower samples to accurately map pixel dimensions to real-world measurements. For more complex stem detection, machine learning models might be trained on a diverse dataset of cauliflower images.
Findings and Discussion
The implementation of the image processing-based cauliflower stem cutting machine yielded significant improvements:
Enhanced Accuracy and Consistency: The system consistently achieved stem cuts within a tolerance of ±2 mm, a remarkable improvement over manual methods, which often varied by ±10 mm or more. This led to highly uniform products, desirable for retail packaging.
Increased Throughput: The automated system processed cauliflowers at a rate of 30-40 units per minute, a substantial increase compared to 10-15 units per minute by skilled human operators. This significantly boosted overall production line efficiency.
Reduced Labor Costs: The need for manual stem cutting labor was drastically reduced, allowing personnel to be reallocated to other value-added tasks.
Minimized Product Waste: Precise cutting reduced the amount of usable cauliflower head inadvertently removed with the stem, leading to an estimated 5-7% reduction in product waste.
Improved Hygiene: Automation reduced direct human contact with the product, contributing to better food safety standards.
Adaptability: The software could be easily reconfigured to adjust desired stem lengths based on different product specifications or market demands, offering greater flexibility.
Conclusion
This case study demonstrates the profound impact of integrating image processing and automation in food processing. The automated cauliflower stem cutting machine successfully addressed the challenges of inconsistency, low throughput, and high labor costs associated with manual methods. By precisely measuring cauliflower dimensions and detecting stem length, the system enables accurate and efficient cutting, leading to a more uniform, higher-quality product ready for packing.
This technology serves as a powerful example of how computer vision can revolutionize agricultural processing, paving the way for smarter, more sustainable, and more efficient food production systems. Further advancements could include integrating 3D imaging for even more complex geometries or incorporating defect detection alongside cutting.
For Rent
Cauliflower Stem Cutting Machine
Get in touch
